Why Spare Parts Procurement Needs an Update: Trends in Purchasing 4.0
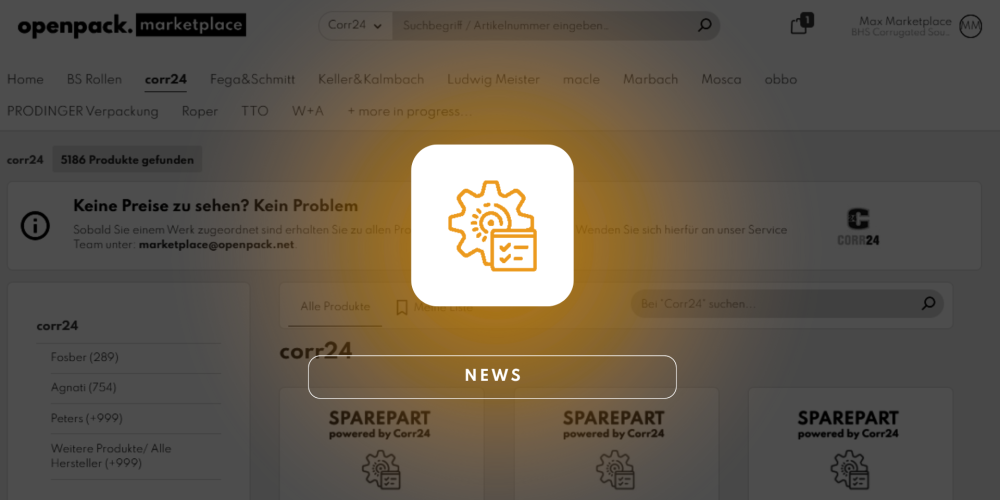
A Look into Production Halls, where Purchasing is often still analog
A defective bearing, a torn seal or a failed control unit is enough to bring entire production lines to a standstill. At such moments, the procurement of spare parts determines whether machines will be up and running again quickly, or whether expensive downtime will occur.
Despite state-of-the-art machinery, many spare parts procurement processes are still surprisingly analogue. Paper-based processes, Excel spreadsheets and phone calls characterise everyday life. However, this is precisely where change is needed: Purchasing 4.0 stands for digital processes that save time, reduce costs, and increase resilience.
Purchasing 4.0: A Strategic Investment in Digital Transformation
The concept of “Purchasing 4.0” has been a subject of much discussion. However, what are the factors that underpin this phenomenon?
The core issue is the intelligent connection of data, systems and people. The objective is not only to digitally map existing processes, but to thoroughly rethink them.
The most important features of Procurement 4.0:
- Digital Data Flows: Information is exchanged automatically between machines, ERP systems and suppliers.
- Transparency through digitalization: Data is available centrally and is therefore always up to date. It is also tailored to relevance and responsibility on an individual basis.
- Proactive Control Systems: designed to identify potential bottlenecks before they arise, ensuring efficient operational management.
- Increased Speed: Processes are automated, ensuring minimal waiting times.
- Early Warning Systems are key to minimizing risk and avoiding business disruptions.
In terms of spare parts procurement, this translates to reduced downtime, minimized storage costs and a more robust supply chain.
Challenges in Traditional Spare Parts Procurement
Anyone who purchases spare parts is only too familiar with the usual hurdles:
- Slow response times: Several days often elapse between notification of requirements, enquiry and order, which is a major problem when machines are down.
- Susceptibility to errors: Manual processes lead to transmission errors, multiple orders or incorrect items.
- Lack of transparency: Who ordered what? Where is the part? When will the delivery arrive? Often, answers to these questions are missing.
- High stock levels: People often buy ‘in stock’ out of fear of running out, which ties up capital and increases storage costs.
Digital solutions can alleviate these issues, but only if companies are prepared to fundamentally rethink their processes.
Automated spare parts procurement: the next evolutionary step
The digital transformation is not limited to the procurement of spare parts. In the current business climate, there is an increasing trend among companies to adopt automated processes. This move is driven by the objective of achieving significant savings in terms of time, financial resources, and other assets. Automation encompasses a wide range of processes, extending well beyond the scope of basic digital order forms.
Core elements of automated spare parts procurement:
- Digital Spare Parts Lists: These parts lists are maintained electronically. This ensures that each spare part is always correctly identified and assigned to its designated machine.
- Live Availability Systems are in place to immediately show whether a spare part is available and how quickly it can be delivered.
- Automatic Demand Messages: Machines are designed to signal independently when components wear out or need to be replaced.
- Initiate Order Proposals or utilize Auto-Ordering Mechanisms: Intelligent software automatically generates order proposals or triggers orders directly.
- Supplier Integration: Digital interfaces facilitate the swift exchange of pricing, delivery times and order statuses.
The result is a significant reduction in manual work, lower error rates and, most importantly, much faster response times when they are needed.
What are the key drivers behind the decision to implement this change?
To successfully navigate the path towards Purchasing 4.0 and automated spare parts procurement, it is essential to implement a clear strategy.
The advantages are significant:
- Time Savings: Automated processes are timesaving and significantly shorten procurement routes.
- Cost Savings: Less warehousing, lower process costs
- Enhanced Purchasing Conditions: Suppliers often grant online discounts
- Competitive Advantage: The digitization of spare parts processes enables companies to act faster and more flexibly than their competitors.
- Better Basis for Decision-Making: Data-based analyses create clarity about requirements, supplier performance and costs.
By transitioning, companies can ensure a stable supply chain and a modern purchasing organization, which is a crucial factor in times of global uncertainty.
Challenges on the path to Purchasing 4.0
Of course, the transition to full automation is not guaranteed to be successful, and the process will take time. Many companies are still struggling with incomplete or outdated master data. Different systems often use different languages, which can cause media disruptions. Furthermore, it is essential for employees to develop a sense of confidence in new automated processes. Initial implementation of new systems is often accompanied by expenses related to time and financial resources, including training.
However, addressing these challenges is crucial, particularly considering the escalating market volatility.
A forward-looking perspective
The development of Purchasing 4.0 and the procurement of spare parts is still in its infancy. However, many exciting developments have long been visible. Some of these are already a reality and will continue to gain in importance in the future:
- Artificial Intelligence: Systems are learning to predict requirements ever more precisely and trigger orders automatically.
- Digital Twins: Virtual images of machines, including all spare parts, enable the implementation of precise maintenance and procurement strategies.
- Blockchain Technologies: In the current business environment, the importance of tamper-proof supply chains and transparent proof of origin is increasing.
- Platform Economy: Digital marketplaces provide a platform for buyers and sellers of spare parts, offering transparency and choice.
It is evident that the future of spare parts procurement will be characterized by increased efficiency, intelligence, and data-driven decision-making.
Conclusion: Purchasing 4.0 is not merely a passing trend …
… it is an essential component of modern business strategy.
Purchasing 4.0 is no longer a vision, but a necessary step for companies that wish to remain competitive in the future. Procurement of spare parts has the potential to streamline processes, reduce costs and ensure machine uptime.
Digitalization is a key driver of competitiveness in the business world. Companies that prioritize and implement digital strategies gain a significant advantage, impacting not only their technological capabilities but also their economic and strategic positioning.